I am new to messing with Polycarbonate. I am making a 1 piece windshield covering the front and both sides. In the picture is some mock up 1/16" material, but I will eventually use 3/16" for the final windshield.
It is hard to tell from the picture, but the windshield will bend over the 1.5" tubing at roughly a 45 degree angle covering both sides.
My bending brake is too small to handle this piece, so I was thinking use heat gun to bend it in place on the frame. The frame is already powder coated.
first question. I know powder can handle some heat, but can it handle the heat created from using a heat gun while bending the material over it? I assume it would, but you never know until you know.
Also, for securing the final windshield in place, What would recommend for hardware and what kind of spacing? I don't want to use rivets. it would need to handle the limits of the car which would be 180+mph.
thanks, kyle
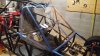
It is hard to tell from the picture, but the windshield will bend over the 1.5" tubing at roughly a 45 degree angle covering both sides.
My bending brake is too small to handle this piece, so I was thinking use heat gun to bend it in place on the frame. The frame is already powder coated.
first question. I know powder can handle some heat, but can it handle the heat created from using a heat gun while bending the material over it? I assume it would, but you never know until you know.
Also, for securing the final windshield in place, What would recommend for hardware and what kind of spacing? I don't want to use rivets. it would need to handle the limits of the car which would be 180+mph.
thanks, kyle
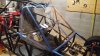
Last edited by a moderator: